Haomei Machinery > Haomei News > Views
How Does Mixer Trucks Work?
Writer:Admin Time:15/01/29Modern concrete consists primarily of four components: Portland cement, sand, gravel and water. A common misconception with concrete is that it dries and gets hard. Actually, the hydraulic cement reacts with the water in a chemical process called hydration. As an example, concrete mixer can be placed underwater and will still change from a liquid state to a solid state and achieve full strength.
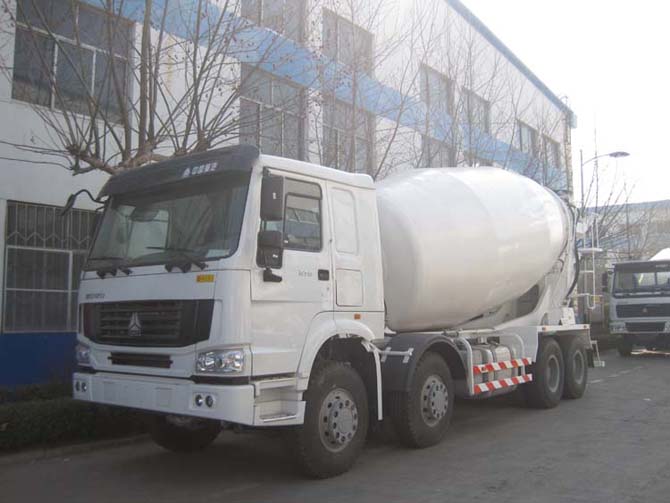
Many additional ingredients can be added to the basic concrete mixer truck in order to change the properties of the resulting concrete. The following list shows some common admixtures (additives) and additional ingredients and their basic purposes:
Admixtures
Accelerators speed up the hydration, or hardening, of the wet concrete. Often used in colder temperatures so the concrete crew has less waiting time between placing and finishing the concrete.
Retarders slow the hydration, or hardening, of the wet concrete. Often used in hotter temperatures so the concrete doesn’t set too quickly, allowing the concrete finishing crew to get the proper finishing work completed.
Air entraining agents add and help distribute tiny air bubbles throughout the concrete. These tiny air bubbles help the concrete resist the freeze-thaw cycles with much less cracking and damage.
Plasticizers and Superplasticizers improve the workability of the concrete during the wet (or plastic) stage allowing the concrete to flow more easily. They are particularly helpful when placing concrete around congested rebar arrangements. Alternatively, Plasticizers and Superplasticizers can be used to lower the water content in the mixer trucks hile keeping a decent level of workability.
Pigments change the color of the concrete for aesthetic reasons.
Additions
Fly Ash can replace about half of the required amount of Portland cement. Fly Ash is a by product of coal fired electric generating plants, so is often readily available and economical. Concrete made with Fly Ash and Portland cement mixer can have higher strength and improved chemical resistance and durability. The use of Fly Ash concrete is considered environmentally sound, since most fly ash otherwise ends up in landfills and the energy to produce the replaced Portland cement can also be saved.
Ground granulated blastfurnace slag (GGBS or GGBFS) can also replace part of the required Portland cement. GGBS is a by product of the steel production process. GGBS has had the most use in Europe and Asia.
Silica Fume can also replace part of the required Portland cement. Silica Fume is a by product of the manufacture of silica alloys. The particle size of Silica Fume is 100 times smaller than that of Portland cement. Silica Fume improves concrete strength, abrasion resistance and corrosion resistance to chemicals, particularly to salts.